Ever-rising customer expectations are driving unprecedented demand for new product packaging configurations and changing retail formats. As a result, it’s never been more important for consumer packaged goods (CPG) companies to reduce the time it takes to change over their packaging line equipment from one product to another.
Here at Serpa, we target a ’15-minute changeover’ with our customers. While achieving that 15-minute goal is not possible for every application, minimizing changeover times is crucial to boosting productivity and reducing overall operational costs.
There is no single ‘key’ to reducing changeover times — success requires an ongoing commitment to best practices and continuous improvement. Here are four ways companies can improve their changeover performance:
1: Develop a Detailed Understanding of the Current Process
It’s critical to break down and document your current changeover practices in detail. What are the steps operators are performing, and in what order? What tools are required, and are all of those tools easily accessible? What are the most significant delays in the process?
When running multiple shifts, it’s also important to benchmark all teams against your best-performing crew. Remember Peter Drucker’s axiom: “If you can’t measure it, you can’t improve it.” Take the time to interview your operators and engineers. What best practices do your top team employ that can be adopted across the entire operation? Another excellent source of best practices is your packaging solution manufacturer. At Serpa, our sales and technical teams work with our customers on an ongoing basis to refine and improve their changeover processes.
Finally, a single improvement in changeover times is not enough. With so many variable elements — technology, staff, business requirements — you should conduct your process review on an ongoing basis, not a one-off event. It’s vital to revisit your changeover practices on a regular timetable if you want to secure further improvements.
2. Limit the ‘Human Error’ Factor
Perhaps the greatest cause of variability in changeover times is the human element. Many operators have their own way of doing things when ‘tuning’ packaging equipment, but that leads to inconsistent and unpredictable performance across shifts. Instead, it’s essential to determine, document, and reinforce standardized changeover practices. Operator turnover and new hire onboarding only add to this challenge.
Training is an all-important factor in achieving reliable, repeatable changeover performance. New hires must be taught the standard ‘company’ methodologies for changeovers, and ongoing coaching and refresher training for all will serve to reinforce those standardized procedures while introducing new enhancements.
As part of an annual maintenance plan, Serpa can place technicians on-site to assist in delivering this training and establishing changeover best practices.
3. Leverage Automation and Technology
Legacy packaging solutions require manual adjustments that often lead to time-consuming errors during the changeover process. Modern systems, however, incorporate technology that can minimize or eliminate those errors.
Serpa’s Verified Changeover solution, for example, uses a simple Human Machine Interface (HMI) and electronic position indicators to eradicate changeover errors. Each position indicator displays the current value of the changeover point, the target value, and the changeover status. If the actual and target values do not match, the machine will not start.
Another example of technology replacing outdated changeover practices is the use of semi-automatic changeover solutions. The operator uses software to adjust machine settings rather than making manual changes, speeding up the process while minimizing the possibility of operator error.
Customers can also work directly with Serpa to build fully customized and automated changeover systems. Tailored to each organization’s unique specifications, these custom packaging equipment solutions undergo stringent factory validation testing before implementation in the production environment.
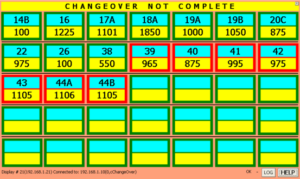
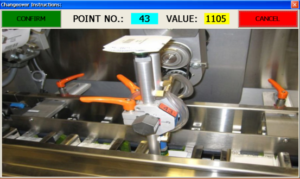
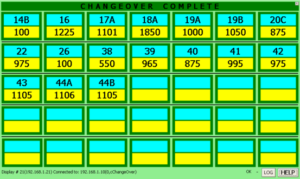
4. Implement a Comprehensive Maintenance Program
Manufacturer support plans can help minimize downtime in many ways, from providing expedited replacement parts to readily-accessible technical assistance. Serpa offers 24-hour turnaround on emergency parts, online troubleshooting, and fast, toll-free technical support.
Regularly scheduled maintenance is also critical for automated packaging systems. Serpa provides a range of preventative maintenance services that help minimize changeover time by ensuring that all equipment is properly configured and functioning optimally.
Achieving Faster Changeovers Requires a 360° Approach
In its 2019 ‘Vision 2025’ report, the Association for Packaging and Processing Technologies (PMMI) found that the lack of repeatability in delivering fast, efficient changeovers was one of the most significant challenges faced by responding companies.
To meet this challenge, companies need to look beyond their packaging technology solutions. They must develop a detailed understanding of both their processes and the human variables within their operation. Documented, standard procedures and ongoing training are at least as important as technical ‘feeds and speeds.’ Finally, a comprehensive, manufacturer support program should be a key component of any strategy to reduce downtime.